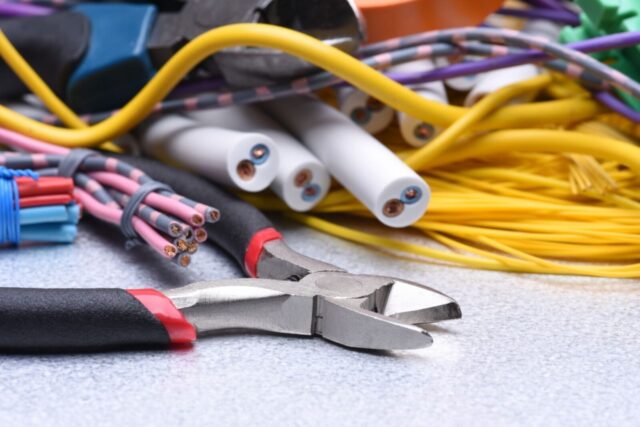
Electrical insulation materials are, arguably, the unsung heroes of the electrical world. Though invisible to most users, their role in safeguarding electronic systems from damage due to heat, vibration, and moisture is essential. This vital component ensures that electrical energy flows smoothly, minimizing loss and enhancing safety.
This guide takes you on an exploration journey to unravel the complex yet fascinating world of electrical insulation materials. From common types, their inherent properties, and applications, to the intricate processes of manufacturing and testing, we will delve into each aspect.
About Electrical Insulation
Our journey begins with the fundamentals. What are electrical insulation materials? Simply put, these are materials impervious to electric current. They hinder the free flow of electrons, thereby preventing the uncontrolled spread of electricity. This feature, in turn, allows the current to follow a specified path.
Not just that, these insulators also provide a protective layer around conductors, preventing potential electric shocks and electrical fires. Considering their vital role, it becomes clear why an understanding of these materials is crucial for anyone involved in electrical applications.
Different Types
There is a plethora of materials used for electrical insulation, each with its unique properties and applications. The vast world of insulation materials can be broadly classified into organic and inorganic substances. Organic insulators are derived from plants or animals, examples of which include paper, wood, and some types of rubber.
On the flip side, inorganic insulators are created from mineral sources. Glass, ceramics, and mica are a few examples. However, both these categories further branch into a multitude of sub-types. Each one is tailored for specific applications, necessitating a keen understanding of their properties and capabilities.
Properties and Characteristics
Each of the insulation materials possesses a unique set of characteristics that makes it suited for certain applications. A crucial trait of these materials is the dielectric strength or the maximum electric field they can withstand before breaking down. Other significant characteristics include thermal stability, moisture resistance, and mechanical strength.
Nonetheless, the physicochemical properties alone don’t make an insulator fit for all purposes. They must also exhibit excellent fire-retardant properties. What is more, they should be resistant to chemical and environmental degradation, ensuring durability and long-term performance.
Common Applications
The realm of electrical insulation sage is wide-ranging. On one end, there are household appliances like refrigerators, televisions, and microwaves, all of which require some form of electrical insulation. On the other, they’re vital in industrial machines, power transformers, and electrical power lines, all of which are crucial if there is to be enough electricity for a system to operate optimally.
The selection of a specific insulating material is guided by the application’s unique requirements. For example, high-voltage applications typically require insulation materials with high dielectric strength. At the same time, insulation for devices that operate in high-temperature environments must have exceptional thermal resistance.
Factors to Consider in the Selection
Choosing the suitable insulation material necessitates careful consideration of various factors. These can range from the operating environment, and electrical properties, to the required lifespan of the product. For instance, in applications where the material may be exposed to moisture, water-resistant insulating materials are the go-to choice.
Further, physical properties like tensile strength, flexibility, and the ability to withstand environmental degradation play a crucial role in the selection process. Economic factors, including the cost of the material and its availability, are other important considerations. After all, the best one is of no use if it isn’t available or affordable.
Manufacturing Processes
The process of manufacturing insulation materials varies significantly depending on the type of material. For organic insulators like rubber or plastic, the process might involve polymerization, a chemical reaction leading to the formation of polymers, followed by a molding process to give it the desired shape.
In contrast, the manufacturing of inorganic insulation materials, such as ceramic or glass, could involve processes like sintering, where the material is heated to just below its melting point until its particles stick together. No matter the process, the aim is always to produce a material that effectively resists electrical current and withstands the environmental conditions it will be exposed to.
Testing and Evaluation
Every insulator needs to go through rigorous testing and evaluation to ensure it performs as expected in its intended application. These tests may include dielectric strength testing, thermal resistance testing, and moisture absorption testing, among others. Do not underestimate the importance of properly testing something before using it. It needs to check all the boxes if it is to fulfill its function.
Aside from these, insulators may also undergo fire resistance tests and mechanical strength tests. These evaluations are vital to ensure the safety and efficiency of the insulating material. Only when a material passes these rigorous tests can it be deemed fit for electrical applications and be utilized in its intended way.
Safety Considerations
Insulation materials’ role in enhancing electrical system safety cannot be overstated. By preventing current leakage and electrical shocks, these materials protect both the equipment and the users. However, to guarantee safety, it is crucial to select the right material and ensure it is properly installed and maintained.
Moreover, it’s important to periodically inspect and replace worn-out insulation to prevent potential electrical hazards. Another critical aspect is following safety protocols during the installation and replacement of insulation. Using the right tools and protective gear ensures safety for the individuals involved in these processes.
Summary
Electrical insulation is pivotal to the functioning and safety of our electrical systems. Understanding their types, properties, applications, and considerations for their selection is vital for anyone involved in the electrical world. The next time you switch on an electrical appliance, remember, there is an insulation material silently working to make your experience safe and efficient. From the unseen corners, they play a major role in energizing our world. Whether you’re an industry professional, a DIY enthusiast, or just an inquisitive mind, we hope this comprehensive guide enlightens your understanding of these vital materials.