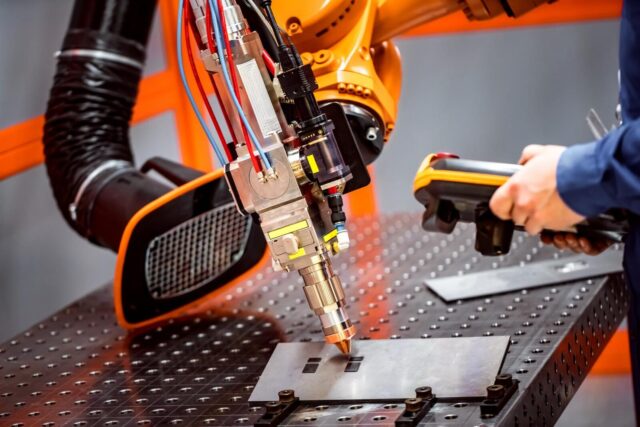
Robotic systems have been a part of the manufacturing industry since the advent of Industry 4.0, increasing production efficiency for high-quality products. Robots now have even more extensive benefits when it comes to deburring. They are no longer only a part of the deburring machine; they are gradually taking over CNC metal machining service to create superior-quality components.
The advent of the “Deburr-Robot-Cells” and further advanced robotic sensing technologies have led to further improvements in the deburring process. Recently, manufacturers have used robotic deburring processes involving passive compliance. This means that the fixed tools and the robot work independently of each other. In this process, the robot is programmed to grip the workpiece and move it to the fixed tools.
Improved technologies have provided the opportunity for active compliance to be engineered into the tools. This ensures a more precise deburring process involving the robot to guide the tools. However, the term deburring may no longer be accurate for such CNC metal machining operations. It is more a matter of metal cutting or metal edge shaping using solid end mills with chamfers up to 5 millimeters.
The Robotic Deburring Process
There are several carefully planned steps involved in using robots to remove excess material or burrs from the edges or surfaces of workpieces. Here’s a detailed breakdown of each step:
1. Planning
This step involves identifying parts that may require deburring. The parts are carefully inspected by experts to determine the type and extent of the imperfections. Such information is crucial for the other planning processes, including tool selection and robot programming. The appropriate tool (end mill, drill, or abrasive disc) is selected based on the material that requires deburring and the shape of the manufactured component.
Choosing the right metal CNC machine for deburring isn’t just about the process itself; it must fit your overall fabrication plan. One tool is a double-sided deburring machine with two coated abrasive flap wheels with large diameters that turn in opposite directions. It can handle CNC metal up to 0.2 inches thick in one operation. It can also be adjusted with various flap wheels, ranging from 40-grit to 120-grit, depending on your desired finish.
For thicker materials, consider a precision faceting and beveling machine suitable for a wide range of metals. Such machines can carry out beveling along with cross-grinding, resulting in zero opposite burr. As a result, you can get infinitely adjustable beveling angles from 30 degrees to 60 degrees. You can also get an adjustable facet width from 0 to 3⁄8 inches.
Consider a machine with a fixed 45-degree beveling angle and an adjustable beveling width if it suits your needs. Such machines are low-maintenance options, operated by one person, and work on 220- or 440 volts power. Integrating deburring machines directly into your fabrication process is ideal, if possible, to increase efficiency and safety.
2. Programming
Once the right tool is selected and an adequate deburring plan is in place, the next step involves programming the robot. This involves defining the toolpath and specifying the speed, force, feed rate, and orientation of the robot’s end effector. The developed program can then be uploaded to the robot controller that guides the robot during the operation.
However, the programming process may not be very straightforward, especially for robot-assisted mechanical processing operations. New deburring process parameter control and tool path planning methods are now possible with the development of hybrid robot manipulators with a high degree of freedom. These hybrid options can work adequately with 6-axis industrial robots, ensuring all exposed sides of a CNC metal are easily reached.
The process development team must determine the parameters to be optimized. At the same time, the programming should compensate for deviations from ideal tool paths at reversal points.
3. Execution
The deburring process can begin with the right plan and program in place. Generally, the robot’s end effector, typically a cutting tool or abrasive disc, is positioned over the part. It then moves in a predetermined pattern to remove the burrs. The robot may use techniques like polishing, brushing, grinding, or sanding, depending on the nature of the burrs and the type of material.
We can break down the process into the following stages:
- Part Loading. The parts are loaded into the work cell or fixture. Newly developed robotic systems make room for easy automatic loading. The gripper picks up the part from the pallet and places it on the feed table of the machine.
- Part Positioning. This step is essential so the robot can accurately locate the burrs and imperfections. Jigs and fixtures can help hold the workpiece in place while the robot deburrs. This is relatively easy because transition movements and approach paths have been predefined during the planning stage. Whenever a workpiece is out of tolerance, the corresponding tool and workpiece coordinates can be quickly and easily corrected.
- Inspection. After the deburring process, the parts are inspected to ensure that there are no burrs left. The robots often come with cameras and sensors that enable quicker automated inspection. Coordinate measuring machines or 3D scanners are also excellent options for inspection. The system can address any remaining burrs before preparing the part for the next production stage.
- Part unloading. After inspection, the workpiece is unloaded from the work cell or fixture. The automated conveyor helps to perform this action, ensuring zero damage or contamination after deburring.
Conclusion
Relying on robotic deburring allows CNC metal machining companies to meet quality and performance demands on various products. Robotic deburring tools offer a compelling combination of efficiency, reliability, and safety, making them versatile and attractive options for a wide range of processes. The automated systems ensure a high level of consistency along with high throughput levels. They ensure faster processing, increased output, cost-effectiveness, and improved profitability.
With newly developed sensors and fixturing technologies, robots are more capable of deburring and machining metal than ever before.